Multiaxis Links
Introduction
The Link tab of the Multiaxis Wizard contains all of the parameters for defining the link moves. Separate sections are provided that allow specific control based on the type of move. The parameters are used in conjunction with the Retracts and Default Lead-In/Out dialog boxes.
Entry/Exit
First Entry
-
Approach from clearance area - uses the area specified in the Retracts dialog box.
-
Approach from rapid distance - uses the rapid distance specified in the Retracts dialog box.
-
Approach from feed distance - uses the feed distance specified in the Retracts dialog box.
-
Direct - applies an approach to the drive surface with no lead-in or lead-out. The feedrate is rapid. The tool axis orientation during direct entry is the Z-axis.
-
Approach from Incremental Clearance Plane - uses the specified incremental clearance distance from the Retracts dialog box.
Last Exit
-
Retract to clearance area - uses the clearance distance specified in the Retracts dialog box.
-
Retract to rapid distance - uses the rapid distance specified in the Retracts dialog box.
-
Retract to feed distance - uses the feed distance specifies in the Retracts dialog box.
-
Retract to clearance area through tube centerr - retracts the tool to the Clearance Area through the center of a tube.
-
Direct - applies an exit from the drive face with no lead-in or lead-out. The feedrate is rapid. The tool axis orientation during direct exit is the Z-axis.
-
Retract to Incremental Clearance Plane - uses the specified incremental clearance distance from the Retracts dialog box. This allows you to reduce clearance movements when the tool can safely perform rapid movement below the clearance plane.
The tool Home Position for the feature is specified in the Retracts dialog box which is accessed from the Link tab. You must first select one of the following options to make the XYZ home position values available in the Retracts dialog box.
-
Start from Home Position
Select the check box to start the approach from the home position.
Clear the check box when not starting the approach from the home position.
-
Return to Home Position
Select the check box to return the tool to its home position after the
operation.
Clear this check when not sending the tool to the home position after
the operation.
Gaps Along Cut
The Small Gaps and Large Gaps items share the same options as listed next.
-
Direct - treats the gap as if it doesn't exist and links the toolpath segments directly with no retract.
-
Follow surfaces - attempts to follow the geometry surface and create a toolpath as if the geometry is closed.
-
Blend spline - creates a spline that is blended between the two surfaces to link the toolpath segments:
-
Step - creates a step to link toolpath segments when needed.
-
Retract to feed distance - causes the tool to retract to the Feed distance value before connecting to the next toolpath segment.
-
Retract to rapid distance - causes the tool to retract to the Rapid distance value before connecting to the next toolpath segment.
-
Retract to clearance area - causes the tool to retract to the Clearance area before connecting to the next toolpath segment.
-
Retract to Incremental Clearance Plane - uses the specified incremental clearance distance from the Retracts dialog box. This allows you to reduce clearance movements when the tool can safely perform rapid movement below the clearance plane.
-
Follow Stock - uses the stock geometry shape to perform linking motions. This is only available when the Stock Definition check box is selected in the Roughing tab.
Small Gap Size - sets the threshold size for small gaps in one of two ways.
-
In % of Tool Diameter - is a percentage of the tool diameter.
-
As Value - determines the actual size of small gaps.
The following image shows small gaps (3) with Direct selected, and large gaps (4) with Retract to Feed Distance (2).
Links Between Slice
The Small Moves and Large Moves items share the same options as listed next.
-
Direct - links the toolpath segments directly with no retract.
-
Follow surfaces - links the toolpath segments by following the surface. You must have gouge checking activated to use this option.
-
Blend spline - creates a spline that connects the two toolpath segments.
-
Step - creates a step to link toolpath segments when needed.
-
Retract to feed distance - causes the tool to retract to the Feed distance value before connecting to the next toolpath segment.
-
Retract to rapid distance - causes the tool to retract to the Rapid distance value before connecting to the next toolpath segment.
-
Retract to clearance area - causes the tool to retract to the Clearance area before connecting to the next toolpath segment.
-
Retract to Incremental Clearance Plane - uses the specified incremental clearance distance from the Retracts dialog box. This allows you to reduce clearance movements when the tool can safely perform rapid movement below the clearance plane.
-
Follow Stock - uses the stock geometry shape to perform linking motions. This is only available when the Stock Definition check box is selected in the Roughing tab.
Small Move Size - sets the threshold size for small moves in one of two ways.
-
In % of Tool Diameter - is a percentage of the tool diameter.
-
As Value - determines the actual size of small moves.
The following image shows small moves (1) with Direct selected, and large gaps (2) with Retract to Feed Distance.
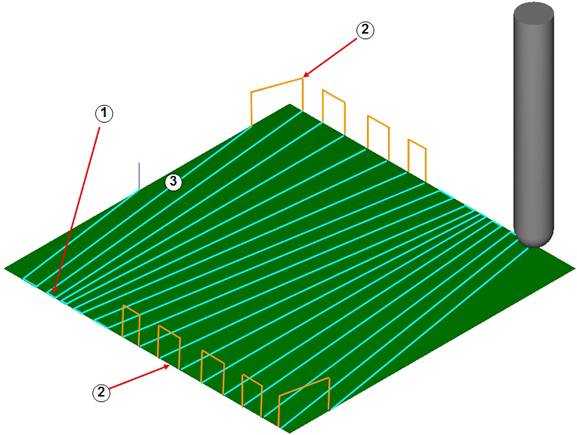
Links Between Passes/Layers
Most of the toolpath types use Passes when moving from depth pass, to depth pass. When using the Swarf Machining toolpath type, this is referred to as Layers.
The Small Moves and Large Moves items share the same options as listed next.
-
Direct - links the toolpath passes directly with no retract.
-
Follow surfaces - links the toolpath passes by following the surface.
-
Blend spline - creates a spline that connects the two toolpath passes.
-
Step - creates a step to link toolpath passes when needed.
-
Retract to feed distance - causes the tool to retract to the Feed distance value before connecting to the next toolpath pass.
-
Retract to rapid distance - causes the tool to retract to the Rapid distance value before connecting to the next toolpath pass.
-
Retract to clearance area - causes the tool to retract to the Clearance area before connecting to the next toolpath pass.
-
Retract to Incremental Clearance Plane - uses the specified incremental clearance distance from the Retracts dialog box. This allows you to reduce clearance movements when the tool can safely perform rapid movement below the clearance plane.
-
Clearance blend spline - enables two contours to be linked with a new blend spline.
-
Follow Stock - uses the stock geometry shape to perform linking motions. This is only available when the Stock Definition check box is selected in the Roughing tab.
Small Move as Value - sets the threshold size for small moves.
-
As Value - select this option and then type a value to determine the actual size of small moves.
Links between regions
When using the Swarf Machining toolpath type, this is group becomes available.
The Small Moves and Large Moves items share the same options as listed next.
-
Direct - links the toolpath passes directly with no retract.
-
Follow surfaces - links the toolpath passes by following the surface.
-
Blend spline - creates a spline that connects the two toolpath passes.
-
Retract to feed distance - causes the tool to retract to the Feed distance value before connecting to the next toolpath pass.
-
Retract to rapid distance - causes the tool to retract to the Rapid distance value before connecting to the next toolpath pass.
-
Retract to rapid distance - causes the tool to retract to the Clearance area before connecting to the next toolpath pass.
-
Retract to incremental clearance plane - uses the specified incremental clearance distance from the Retracts dialog box. This allows you to reduce clearance movements when the tool can safely perform rapid movement below the clearance plane.
-
Clearance blend spline - enables two contours to be linked with a new blend spline.
Small Move as Value - sets the threshold size for small moves.
-
As Value - select this option and then type a value to determine the actual size of small moves.
Leads
Next to all of the Link options that are described in this help topic are the following lead options.
-
Use Lead-In - select this option to use a lead-in only.
-
Use Lead-Out - select this option to use a lead-out only.
-
Use Lead-In/Out - select this option to use a lead-in and lead-out.
-
Don't use Lead-In/Out - select this option if no leads are needed.
Once you have set any of these options to
use leads, click to
access the Leads parameters. Leads are explained in the Lead-In
Dialog Box topic.
Other Options
-
Click Retracts to open the Retracts dialog box with various clearance plane and distance parameters.
-
Click Default Lead-In/Out to open the Default Lead-In/Out dialog box.