Questions?
Call Us to speak with a CAD CAM Pro!
Questions?
Call Us to speak with a CAD CAM Pro!
Is it worth acquiring CAD/CAM for lathe programming?
Most CNC shops have a lathe, however, not all have CAD CAM for lathe. The difference is astronomical comparing the number of shops that use CAD CAM for Mills vs the number of shops that use CAD CAM for lathes. Milling and machining centers represent more than 80% of CAD CAM users, while for many 2-axis lathes less than 20% are programming with CAD CAM software. So, the question is, why aren’t you using CAD-CAM for lathe? Keep reading to learn the upside or CAD CAM for lathes and why you should program your lathe with CAD CAM.
Why use CAD CAM for Lathe?
2 Axis CNC Lathe programmers are known to say
” The lathe is easy to program using canned cycles, and there is no need to invest in CAD/CAM”
Claiming it would take more time to program the part in the software than at the control or that production of the same part doesn’t require programming. ” We always make the same part” Many users felt the same way until they learn about the upside of CAD CAM for lathe. Today, we will analyze these arguments and determine if it is worth acquiring CAD/CAM for lathe programming.
Canned Cycles / On Board Programming for Lathes
If you have programmed a CNC lathe, you know that cycles like G71 and G72 make the programming process extremely quick and easy. You only need to define the profile to be cut once, add the cylinder size, and define the distance between each pass, and the program can be sent to the machine.
However, we know that by eliminating the software from this process, you’ll gain speed in programming while sacrificing:
Cycle time
Canned cycles and other onboard programming methods offer simple and effective ways to program part features. Simple doesn’t equal efficiency, often lacking bi-direction cutting and other “limits” used to improve throughput. It’s recommended to test both canned and non-canned cycles for the shortes cycle times, with non-canned processes often running faster.
Air cutting
With limited stock definitions and cut direction control, canned cycles and on-board programming often spend as much time cutting the air as they do cutting material. Using CAD CAM to restrict toolpath while adding bi-directional cutting in some cases can improve part throughput up to 3X.
Collision avoidance
A huge benefit of CAD CAM software for lathes is the ability to define tool inserts and holders adding them to your toolpath development process. Where onboard programming any providing an insert style and orientation, CAD CAM for lathes add collision checking against both the insert and holder, giving programmers control to cut where they can and ensure they don’t where they can’t.
CAD CAM Optimized for CNC Lathes
A CAD/CAM system like BobCAD CAM has strategies and functions designed to optimize lathe cutting, such as:
Lathe Cutting Pattern
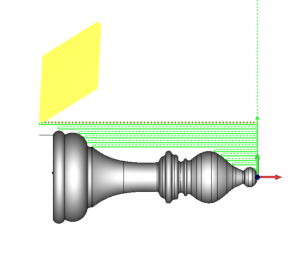
When we program with cycles, we are constantly cutting linearly. The tool enters the cylinder and removes material in a straight motion until it reaches the end of the material, then retracts to the starting position and repeats the process as many times as necessary to rough out the material.
CAD CAM for Lathe Offset Cutting Patterns

Now, when we use CAD/CAM, we have the Offset cutting strategy, which, unlike on-board cycles, instead of linear movements, your tool follows the shape of the final profile throughout the roughing process.
Offset Cutting Pattern Advantages:
- The tool is always in contact with the material, increasing tool life and the quality of roughing.
- By following the shape of the part, the machine makes fewer retractions.
- The toolpath adapts to the shape of the material, eliminating air cutting, which is helpful for unique materials or repairs of existing parts.
- With fewer rapid movements, cutting time is reduced.
Rough Operation:
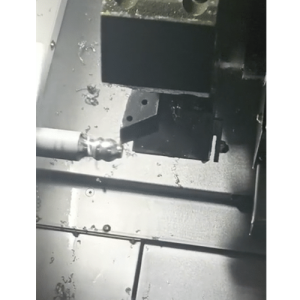
Finished Part:
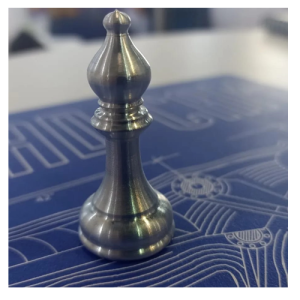
If you have a neutral or circular tool, you can apply a zigzag Offset Path, thus following the shape of the final part and reducing the number of retractions to zero.
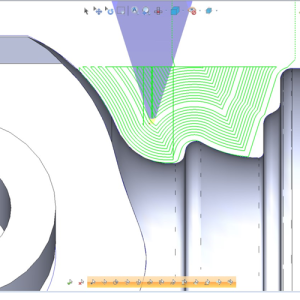
CAD CAM for Lathes Templates
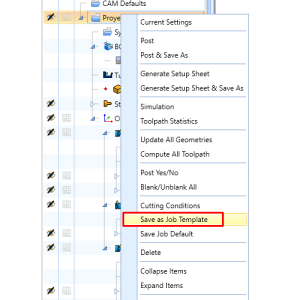
Templates are one of the most straightforward yet valuable functions we have added to our product. If you want to explore this function in depth, we recommend reading “2D Programming with Templates.” Templates allow us to save the processes of any programming within BobCAD CAM, whether it’s plasma, milling, lathe, or EDM.
For lathe, templates represent a direct solution to the argument “I spend more time programming in the software than at the control.” When we have saved a template with all the cutting parameters, such as tools, tool holders, strategy types, step distances, collision checking, speeds, and more, all these parameters are saved from being applied to any other profile with similar properties. In other words, with templates, we only need to program the part once so that every new piece with similar parameters only requires loading the template and selecting the geometry, thereby reducing the programming time from minutes to seconds.
CAD CAM for Lathes Simulation and Collision Checking
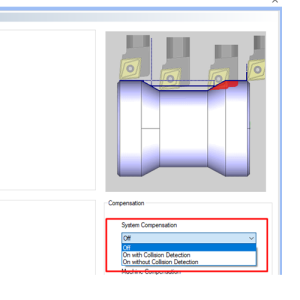
Although this is not one of the most common reasons our users mention for continuing to work at the machine, it is one of the most critical reasons to have CAD/CAM. In many workshops, minor collisions, damages to the workpiece and tool, or tolerance deviations are an everyday occurrence and are considered part of the job. However, that doesn’t mean many collisions or imperfections cannot be avoided. In all lathe strategies in BobCAD CAM, the user can activate Collision Checking and add the tool holder to the checking process. Using this function, BobCAD ensures that neither the insert nor the tool holder will enter areas that could generate collisions.
Furthermore, if any collision occurs outside the strategy, the user can see the collision in our virtual simulation. All toolpaths generated in CAD/CAM will be replicated with the same parameters used on the machine. This doesn’t mean you will never have collisions on your lathe again, but the number of issues you deal with will be significantly reduced.
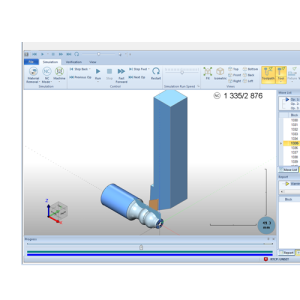
“We do production, and I always make the same part.”
This is the last argument, but if we can apply Templates and Offset to our “same part,” we can program it in seconds, reduce machine time, and improve quality. Therefore, if you are going to program this same part thousands of times, reducing a few seconds on the machine, as well as in post-cut polishing processes and saving on tooling, can represent substantial savings in both time and money.
Conclusion
All these functions will save you money and time, but it depends on the end user. It doesn’t matter if you purchase software for lathe, milling, or 5-axis machines; if you don’t go through the corresponding training process, none of these functions will help. It may be better to continue programming on the machine. Therefore, we invite you to learn and improve your processes because the software will always be better than programming on the machine. However, working on the machine will always be easier if you are familiar with your software or another solution.
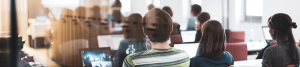
Many resources are available for learning more about programming a 2 Axis CNC lathe. These include online tutorials, user forums, one-on-one, and professional training seminars. CAD CAM software providers often offer training and support to help users get up to speed quickly.
Free Weekly Training Click Here | 1 PM EDT
Over the last 3 years, over 200 new features were added to our CAD CAM software.
Join our weekly training to learn what’s New with BobCAD-CAM, BobCAM for SOLIDWORKS, and BobCAM for RHINO.
Are your machines and projects getting more complicated?
Call Us to speak with a CAD CAM Pro!