Clearwater, Florida – When time is money, BobCAD-CAM’s High Speed Machining really delivers. That’s why professionals like Ken Herring, legendary race car design engineer trust BobCAD-CAM to fill the need for speed by reducing cycle times and cut any part faster than ever before.
Here’s How You Can Increase Your Shop’s Efficiency And Raise Your Bottom Line…
The latest versions of BobCAD-CAM CNC software provide CAM users with an all new High Speed Adaptive machining toolpath that empowers shops to light up their machines with cutting speeds that are significantly higher than ancient offset cutting strategies that have been used before. Most production job shop programs involve basic 2 – 2.5 Axis milling. The more complex the programs get, the longer these CNC machining cycle times become. With the new HS Adaptive machining operations in BobCAD-CAM, you can select a CAD model feature and apply the high speed operations through Dynamic Machining Strategy™ wizards that provide advanced simulation and automatic g-code programming in a matter of minutes.
Meet BobCAD-CAM Software User Ken Herring
Kenneth Herring is the owner of Texas Chassisworks in Tyler, Texas. He’s no stranger to the need for speed. Ken founded Texas Chassisworks in 1999 with the goal of producing high-end turn-key drag cars.
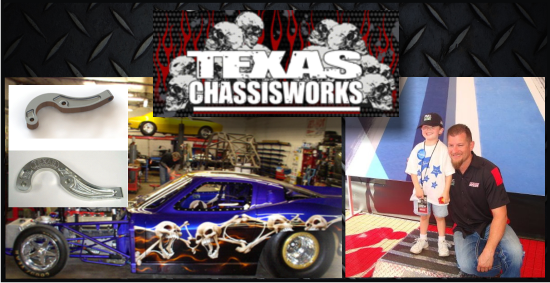
Since then, Ken and his crew have expanded their operations into performing drag car repairs, updates and more with their own CNC billet part line. As an manufacturing business owner, experienced drag racing engineer and Pass Time Speed TV show host, Mr. Herring CNC manufactures many of their automotive and drag car racing parts such as header flanges, turbo parts and his billet steering arms with the BobCAD-CAM software because it’s much faster, easier and less expensive. He was blown away by the speed and efficiency in these high speed machining operations. Recently while using the BobCAD-CAM high speed machining technology to machine header flanges on his HAAS VF 2 he was able to cut down his machine time on the parts pockets by 200%.
“Machining the same pockets with traditional offset pocketing toolpath would have taken 2 1/2 times longer” according to Ken.
The fact that Ken can achieve excellent part finish results in half the time that traditional toolpaths can complete a part is an exceptional value to the high speed adaptive toolpath technology. “BobCAD’s high speed machining is so fast my tooling vendors couldn’t believe their eyes!” he responded when asked about the new Adaptive Roughing operations in his BobCAD-CAM software.
Understanding High Speed Machining
High speed machining is very different than traditional offset type cutter paths. Also known as “trochoidal” toolpath, the Adaptive Roughing cutting strategy allows the user to use the whole cutting edge length of the tool which ensures that the heat and wear are uniformly spread out, leading to longer tool life than traditional slot milling for example. In addition, the controlled arc of engagement between the tool and the material generates lower cutting forces which enable higher axial depths of cuts to take place. Basically, the constant tool engagement allows for deeper cutting without “stop and go” movements in the cutting paths. It’s also a great solution for slot milling and pocketing when vibration and chatter is an issue. This level of high speed CAM technology allows machinists to run their machine’s cutting speeds much higher than usual. Some case studies show a 40% to 50% increase in cutting speeds successfully completing parts with a significant reduction in production cycle times, without compromising at all in the parts finish results. In other words, turn it up with the high speed machine cutter paths and experience substantially improved results from reduced tool wear, better cycle times and less wear and tear on the CNC machine long term.
The difference in the BobCAD-CAM high speed Adaptive Roughing is that it isn’t just for 2.5 Axis part machining any more. BobCAD high speed strategies can be used for full 3 Axis, 4 Axis and for the first time in CAM, full 5 Axis CNC programming. In addition to this breakthrough, the high speed operations are available inside of the systems machining wizards that step users through generating the required toolpath, removing the guesswork. Adaptive Roughing operations are also available in the software’s Dynamic Machining Strategies™ which allow the user to apply any number of machining operations to a single CAD feature. Thus adding more efficiency and speed to CAD-CAM part programming. Due to the fact that machine time is money, you could practically refer to it as “profit machining”.
To add these High Speed Adaptive Toolpaths to your CNC toolkit, contact BobCAD-CAM at 877-262-2231 or 727-442-3554.
You can also Download a FREE demo HERE.
Summary
Article Name
CAD-CAM Software - CNC Machining & The Need for Speed
Description
This article discusses how High Speed CAD-CAM machining technology is positively affecting CNC manufacturing.
Author
BobCAD-CAM, Inc.