Questions? Call Us to speak with a CAD CAM Pro!
A high-speed machining is characterized by removing a large amount of material, using a larger surface of the tool. In the following image, we can see how traditional cutting strategies differ from high speed cutting strategies generated on a CNC machine.
Traditional vs High Speed Pocket Patterns
As we can see, the traditional path performs fewer movements than the high-speed milling pocket, but these have rectangular corners that generate load on the tool and are linked to a linear connection that leaves a mark in the material.
In addition to increasing the load on the tool, the rectangular corners force feed rates to be reduced considerably. Additionally, in traditional machining cutting, only one area of the tool gets wear. This happens because the load is not evenly distributed over the entire circumference of the tool, causing the wear to be only on one side and the depth of cut to be minimized to avoid tool breakage. In the following images we can observe this:
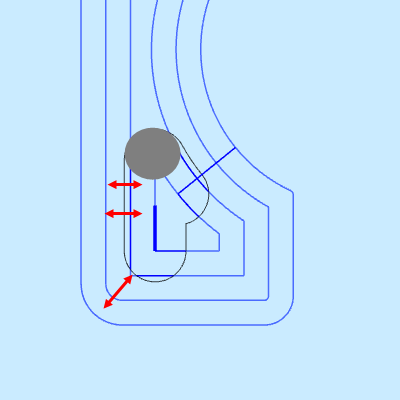
Traditional
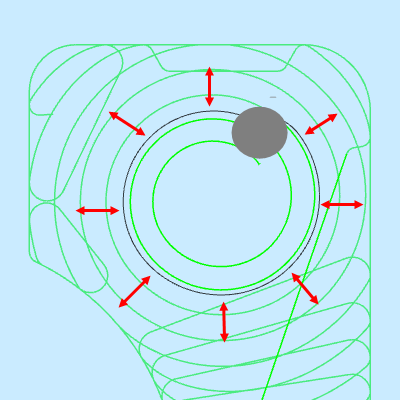
High Speed
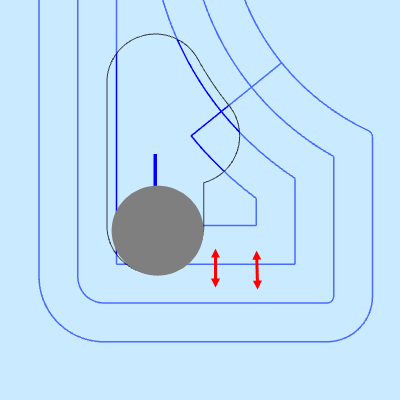
Traditional
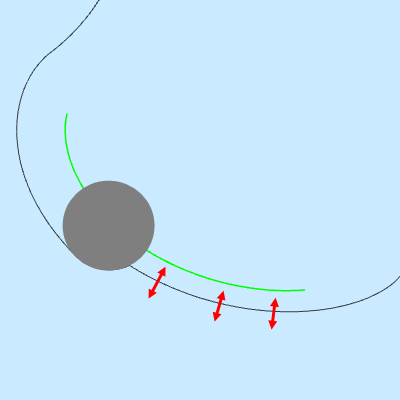
High Speed
Now that we understand the difference between traditional and high-speed strategies, let’s take an in-depth look at the impact on the tool. When a tool cuts material, it generates heat, load and wear. In the following image, we can see how these factors are distributed on the tool, depending on the type of cutting:
Traditional vs High Speed Depth of Cut
When cutting, traditional strategies focus on the tip of the tool, so this part receives all the wear and heat. In high-speed cutting, the wear is spread over the entire cutter body, utilizing its full depth. Load and heat sharing and micro retracts eliminate the need for coolant in machining in most cases, since the cutting edge of the tool does not get as hot and the micro retracts release the pressure and let the chips out.
Regardless of whether you are using an old or new machine, carbide, insert or high-speed tool, this strategy is going to save you money and time every time you need to rough material.
Videos on the subject:
Questions? Call Us to speak with a CAD CAM Pro!
Leave a Reply