Is upgrading to Mill Premium really worth it? If you’re a job shop CAD CAM programmer, why in the world would you ever want to upgrade to Mill Premium? Keep reading and learn how this shop used toolpath technology to save time and win new customers.
Weekly CAD-CAM Training – Join Us Here
BobCAD-CAM | BobCAM for SOLIDWORKS | BobCAM for RHINO
Mill Premium Helps Jobs Shop Win More:
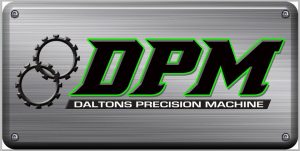
As a long-time shop owner and CNC programmer with a passion for racing, Doug runs his shop just like his laps, as fast and consistently as he can. Often choosing methods known to work vs trying to learn how to do something new.
We try to win new jobs, sometimes that means figuring out how to program them after.
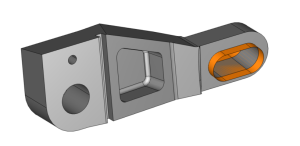
Having the BobCAD CAM software and support has really come in handy over the years, it’s why I keep current.
Challenges of Programming Undercuts with CAD CAM software:
“When you move past simple slots and pockets you get into contoured surfaces, daft and sometimes negative draft, this is where Mill Premium was worth it for me!”
Geometry Editing CAD Features
What CAD features are used often used with toolpath? Working with CAD files or CAD data, CAD CAM starts with geometry and ends with toolpath and g-code. Use these to navigate surface selection and editing geometry when part programming.
Tool Accessibility
Undercuts can present challenges in terms of tool access and reach, especially when working with complex geometries. Toolpath that can effectively navigate and machine undercuts without interference can be a complex task.
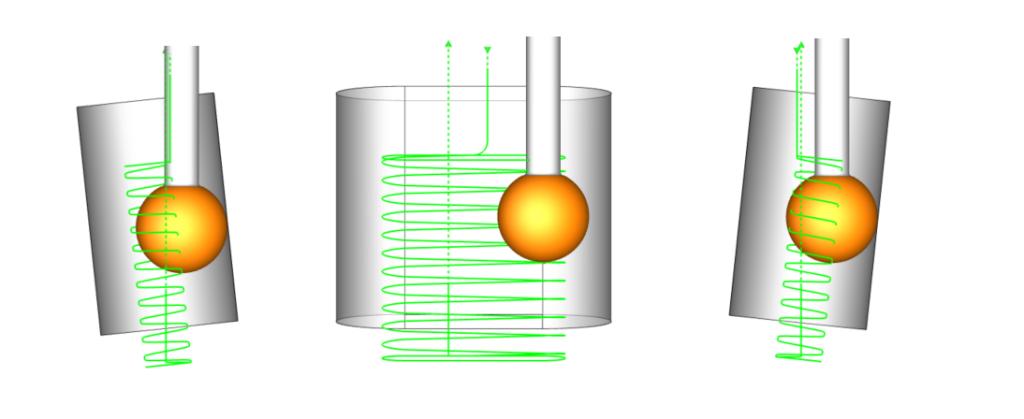
In our example, we are working with a negative draft slot, so our geometry is simple enough, we still need to consider tool clearance on the entry and exit and we also want to make sure we aren’t trying to cut where the tool can’t.
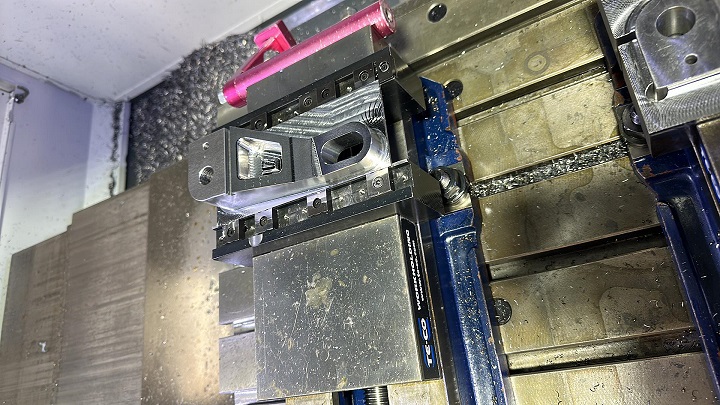
Collision Avoidance:
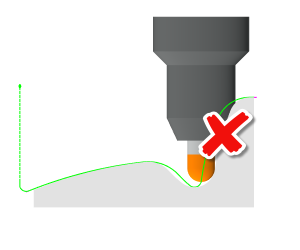
Undercuts may create situations where the tool or holder can collide with the part or fixtures. Ensuring collision-free toolpaths and verifying clearances is crucial to prevent any damage or errors during machining. Mill Professional and Mill Premium packages offer multiple tools to compact collisions which include check surfaces, advanced allowance, and dynamic holder checking.
Tool Selection for Undercutting
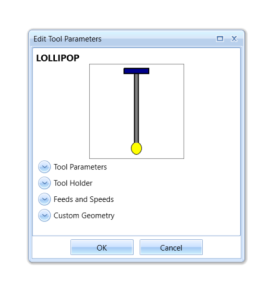
Choosing the right tool for machining undercuts is vital. It should have a suitable geometry and length to reach the undercut regions effectively. Limited tool options or improper tool selection can result in incomplete or inaccurate machining. Choose Mill Preimim to unlock barrel tooling.
Surface-Based Toolpaths For Undercutting
When you upgrade from Mill Professional to Mill Premium you unlock multiple new options, and you get all the newest toolpath technology. Which sounds great, but which one of these new options to do you and why is often the question new users and even long-time programmers have.
Offering more options and control, they achieve greater accuracy and often run faster because of optimization settings, like point distribution and feed zone mapping among other settings.
Machining Strategy for Undercutting :
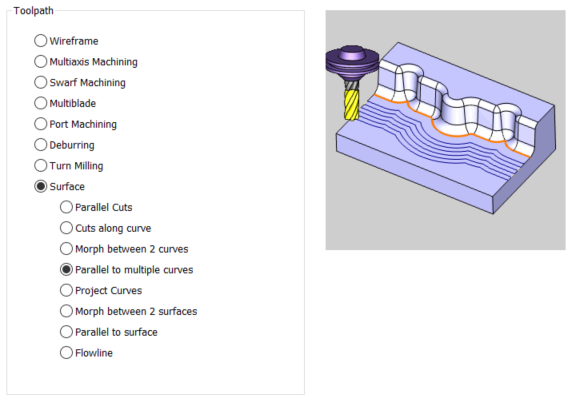
Determining the best machining strategy for undercuts is crucial. It involves deciding whether to use 3-axis, 4-axis, or 5-axis machining techniques based on the complexity of the part geometry. Selecting the appropriate strategy ensures efficient material removal and desired surface finish. In our example, we use parallel to multiple curves. This surface-based toolpath can output 3, 4 or 5 axis based on your software license.
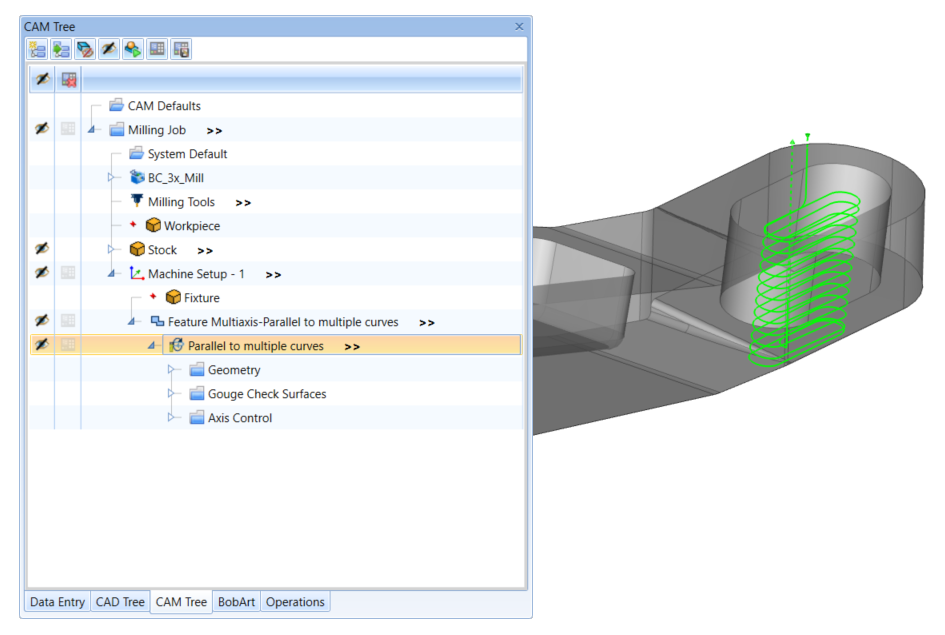
A big reason why ramp profile milling has been a big part of Doug’s shop’s success.
“ Keeping the tool in the cut and cutting is what saves you time on jobs”
So for Doug, this slot needs to be ramping all the way down.
The “play book” for roughing similar components that Doug has manufactured over the years has stayed consistent. Using BobCAD’s profile pattern called contour ramping, he can run the tool around the part profile ramping down. This keeps the tool in the cut and is one of the ways he keeps his cycle times down.
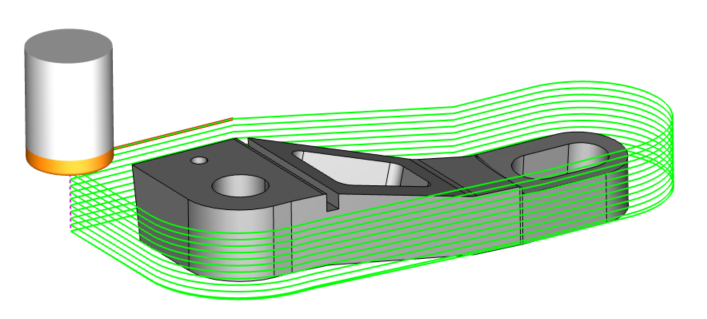
Another Roughing Cycle Doug Often uses is the advanced pocketing feature, this allows him to work his way in from outside the stock using a dotted line boundary to define the stock edge.
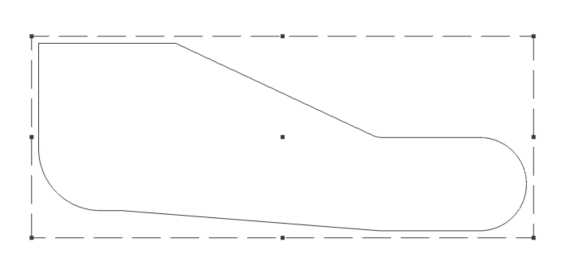
Advanced pocketing cycles will start /plunge outside the dotted line for the entry of a cut.
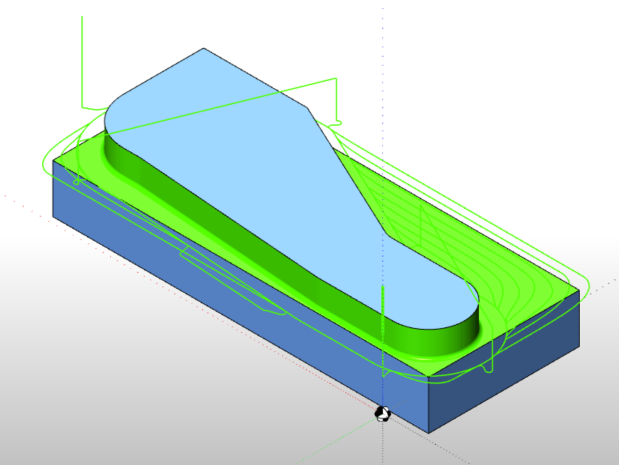

Changes applied in recent releases represent a significant saving of programming and machining time; for this reason, we recommend watching all the training videos, attending all of our webinars/training events, read our blogs, and use your online training. BobCAD is constantly evolving, you may be wasting time and money just due to your lack of knowledge.
Thank you all very much and we look forward to seeing you at the next webinar on this topic:
Mill Professional vs Mill Premium | Choose Premium Best for Undercutting: June 7th @ 1PM
Related Videos:
Getting Started Online Classes – Sign up here it’s Free.
Which toolpath options come with what packages?
Use the toolpath matrix.