In today’s competitive manufacturing landscape, efficiency and precision are more important than ever. For machinists and shop owners looking to streamline their processes and take on more complex projects, having the right tools is essential. That’s where the Mill 3 Axis Premium toolpaths come in. Designed to offer unmatched flexibility, control, and speed, these high-end toolpaths bring the power of advanced multiaxis machining into your 3-axis workflows. Whether you’re handling intricate geometries, automating tedious deburring tasks, or optimizing cutting strategies, our toolpaths empower you to do more—faster and with greater accuracy.
In this blog, we’ll explore a few of the standout features of the Mill 3 Axis Premium toolpaths and how they can revolutionize your machining operations. From sophisticated surface-based operations to efficient deburring processes, we’ll show you how to unlock new levels of performance and productivity in your shop.
Mesh-Based Operations
Steep Shallow Operation
The Steep Shallow operation enables you to handle both steep and shallow areas of a part using two specialized toolpaths in a single operation. This approach ensures that steep features are machined using appropriate strategies while shallow areas benefit from tailored cut styles. By combining the best of both worlds, this operation delivers unparalleled flexibility. Moreover, it offers exceptional speed, calculating up to 78 times faster than traditional methods, which translates into substantial time savings and increased shop productivity.
Z Level + Equidistant |
Z Level + Planar |
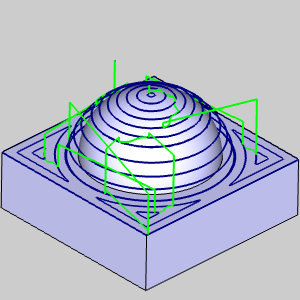 |
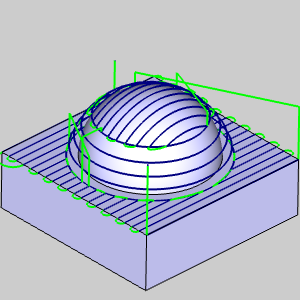 |
.
Independent Cutting Methods
The versatility of the Steep Shallow operation is further enhanced by allowing independent control over the cut direction for steep and shallow areas. You can now assign different milling directions for each aspect, enabling more efficient material removal. This level of control allows for highly optimized toolpaths tailored specifically to the geometry of your part.
Deburring Operations
The Deburring operation streamlines the process of removing sharp edges and burrs from your parts, essential for both safety and part functionality. With automatic feature detection, linking, and collision avoidance, deburring complex parts is effortless. Simply select your tool and geometry, and let the system handle the rest. This operation even supports undercuts when the appropriate tools are selected, reducing the complexity and time required for manual edge selections.
.
Chamfer Tool
In addition to spherical tools, the Chamfer Tool is now fully supported for deburring operations, offering expanded tool options to fit your specific machining needs. Whether using endmills, tapered tools, or chamfer mills, the deburring process is more efficient than ever.
Containment Body
Specify exact deburring areas by selecting a containment body, ensuring that only the desired regions are processed. This eliminates the need for tedious manual selections and allows for precision control over the deburring areas.
Spiralize Closed Contours
Spiralize closed contours smooths transitions between multiple cuts along edges by using a spiral movement instead of linking moves. This results in a cleaner finish, reducing the likelihood of visible marks and improving overall surface quality.
Asymmetric Chamfers & Edge Shapes
This operation supports asymmetric chamfers, allowing you to machine more complex edges at various angles. The feature also works with spherical mills, expanding the range of parts that can be deburred while maintaining high efficiency and precision.
Fixed Tool Contact Points
Control the exact position of the tool’s contact point on cones and cylinders, allowing for precise chamfering. You can set the tool contact from the lowest to the highest point, ensuring uniform chamfers without tilting the tool unnecessarily.
Avoid Contact Point on Tip
To maximize material removal efficiency, the system automatically avoids using the least effective part of the tool—the tip—ensuring optimal cutting performance.
Surface-Based Operations
Flow Direction Control
Flowline toolpaths now offer additional control by allowing you to prioritize U or V directions over traditional long or short side selections. This gives you greater flexibility when machining surfaces, especially in cases where specific flow directions are critical. Though the following animation is shown utilizing multiaxis movement, this can be translated to 3 Axis movements with ease.
Custom Approaches
When precision matters, the Custom Approach option gives you complete control over how the tool enters and exits a cut. Unlike generic options such as approaching from clearance or feed, this feature allows you to define an exact sequence of movements, creating a highly specific approach and retract path for each toolpath. Whether you’re navigating around complex geometries or aiming to optimize toolpath efficiency, the Custom Approach option ensures that you can map out the precise trajectory needed for each operation.
By allowing you to select a specific series of points for the tool to follow, the Custom Approach minimizes unnecessary movements, reduces machining time, and enhances safety by preventing collisions. This level of customization is especially valuable in tight or complex areas where traditional lead options might fall short, giving you unprecedented flexibility and precision in your machining processes.
Feed Control Zone Blending
Smooth transitions between different feed zones are now achievable through the Feed Control Zone Blending feature. By gradually adjusting the cutting speed between zones, abrupt changes in speed can be eliminated, ensuring consistent surface finishes and reduced tool marks.
Run tool at
Project Curves toolpaths now allow precise control over the tool’s contact point, whether on inclined surfaces or other geometries. With full flexibility in selecting cutting side and contact points, you can achieve greater precision in toolpath operations.
Summary of Benefits for Mill 3 Axis Premium
The Mill 3 Axis Premium toolpaths offer unmatched flexibility and control for complex machining operations. Whether handling steep and shallow areas in a single operation, automating deburring processes, or utilizing advanced lead and flow direction controls, these toolpaths empower you to create efficient, precise, and high-quality parts. With faster calculation times and enhanced toolpath customization, your shop can tackle more complex projects while improving overall productivity and reducing machining time.
Questions? Call Us to speak with a CAD CAM Pro!