CAD-CAM software has a reputation for having a steep learning curve when you’re starting on a new software or having to explore new areas of the software to program new job types. For as long as CAD-CAM has been around, developers have faced the challenge of providing increasingly more functionality while continuing to keep the product easy to use. Ask any developer and they’ll tell you that the more features a CNC programming system has, the steeper the learning curve will be. Yet, without CAD-CAM, CNC shops simply cannot stay competitive and efficient.

The CAM Programming Challenge
As a new CNC programmer or as a company thinking of implementing a new CAD-CAM system, the speed at which you’re able to learn the new software should be one of the top considerations in the evaluation process.
The new BobCAD-CAM includes an advanced wizard driven interface that offers a step-by-step programming process – reducing the learning curve, eliminating the guesswork, and improving workflow efficiency.
Typical CAD-CAM Software Workflow
When reviewing the basic CAD-CAM programming workflow, you’ll find it goes something like this:
- Import the part file or complete the design.
- Create the material/stock for the job and origin.
- Create a machine setup or work offset.
- Set up the material type.
- Set up cutting conditions, tool patterns and any machining parameters that apply.
- Select the post processor configuration.
- Start adding machining features, drilling, roughing and finishing toolpaths.
- Build the job in a CAM tree manager.
- Compute and generate all toolpaths.
- Generate the g-code program.
- Simulate.
- RS 232 / DNC send the program to the machine.
There’s a lot of information that goes into the above list in order for CAD-CAM technology to really act smart and create efficient programs. You have to input all that information into the software. Otherwise, you will often times get incorrect results and end up losing valuable time.
So how has CAD-CAM been developed in order to keep it simple and make it so that nothing is left out?
The Solution: CAM Machining Wizards
Wizards are used in the software to properly set something up. In this case, wizards are used for setting up all toolpath and drilling operations within the CAD-CAM system. In a CAD-CAM product, the toolpath wizards should be easily accessible within the Job Tree to keep the job organized. Here you can see an organized location within the Job Tree where all of the toolpath options are listed.
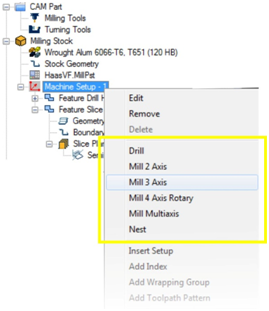
Once a machining strategy is selected the wizard is launched to guide the operator through a proper sequence of steps for creating the toolpath. The wizard driven interface in BobCAD-CAM prompts the user to select the associated geometry to use in the process. Once this is done, the wizard advances to the Dynamic Machining Strategy™ section.

The first benefit of this is having all of your toolpath operations defined and organized into 2, 3, 4, and 5 Axis categories. After selecting the associated CAD geometry for the machining, the user reaches the Dynamic Machining Strategy stage in BobCAD-CAM. In the picture here we have selected Pocketing. This allows for multiple operations to be loaded as part of the machining strategies for the selected geometry. By choosing the “Next” button, the wizard advances to the next section of the wizard, making it quick and easy for the operator. Advanced operators can jump to any section of the wizard just by clicking on any stage in the wizard tree. When finished with all settings, the “Next” button advances the wizard to the next screen.
At this point the wizard allows the operator to create an additional work offset, if needed, or a rotary angle if the program is for a 4th Axis.
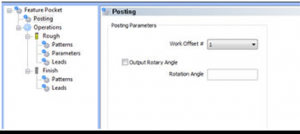
Now the wizard allows the operator to choose and control all of the aspects of the roughing tool. The tool crib and holder database is accessible here in addition to tool data and feeds & speeds which can be customized. Once the roughing tool details are input the “Next” button is selected to advance.
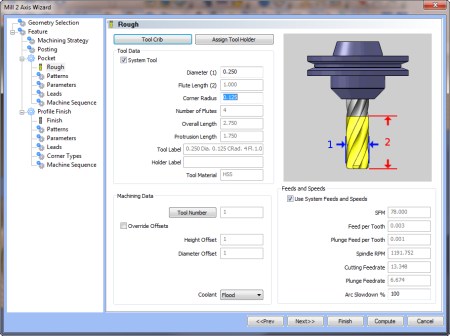
As the user advances through the wizard driven interface, the user can define patterns, parameters, leads and other aspects such as machining sequences and so forth. Different operations will have different screens that relate to the strategy. For example, if a pocketing operation is selected, the wizard will provide a step-by-step process for properly setting up a pocketing operation. Same goes for profiling operations, 3 axis roughing, 3 axis finishing, and so forth.
Here is the Patterns stage of the pocketing wizard below. This is where adaptive high speed options can be chosen for pocketing and more.
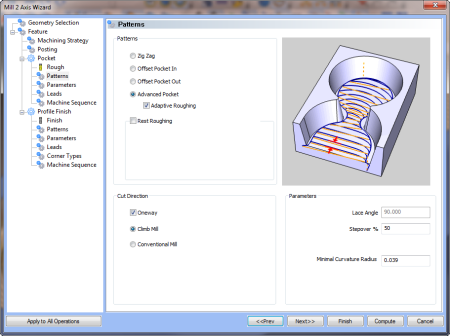
The wizard driven interface provides a step-by-step process for programming simple and complex parts – removing the guesswork from programming. This means that programmers can spend less time figuring things out and more time machining parts.
Try wizard driven technology today in our free demo of the new BobCAD-CAM.

To find out more about CAM Machining wizards contact BobCAD-CAM today at 877-262-2231.
Here are some related CAD-CAM articles you may be interested in:
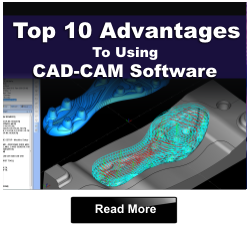
Summary
Article Name
Why is Wizard-Driven Technology so Valuable in CAD-CAM Software?
Description
CAD-CAM software has a reputation for having a steep learning curve but advances in wizard driven interface technology is making it easier than ever to program parts and eliminate the guesswork.
Author
Nick Erickson | BobCAD-CAM