Computer-aided manufacturing (CAM) is a type of software that is used to control machine tools and related machinery in the production of workpieces. Without CAM software, CNC machine shops are generally forced to write machine g-code manually. The g-code is essentially machine coordinates that the programmer tells their machine to send the tool. Depending on the complexity of a part, g-code commands can easily number in the hundreds, thousands, or even tens of thousands. That being said, the actual programming phase can amount to some pretty significant labor hours without CAM programming technology.
The primary purpose of CAM programming technology is to create faster production processes, precision dimensions, and material consistency. In large part, it achieves this by essentially eliminating manual g-code writing. Instead, the CAM software is much more of a visual and intuitive process when compared to writing g-code. At a glance, the user-interface provides a visual representation of the stock (raw material) and 2D or 3D part model from CAD. CAM software uses the stock and part model to subtract material via toolpaths to achieve the desired part geometry.
Incorporating CAM programming technology to a CNC machine shop can completely change a shop’s ability to compete. Eliminating manual g-code writing is a huge boost to productivity and efficiency by itself but the capabilities of advanced CAM software goes well beyond that.
CAM Programming Technology Features That Will Increase Your CNC Program Efficiency
Here are some BobCAD-CAM’s most advanced CAM programming technologies that are changing the CNC programming industry.
Job Tree
The job tree is where all of the machining operations are organized. It provides a clear overview of your machining process which is presented in a drop down menu format similar to the way your PC organizes its drives and folders. This allows you to easily locate and inspect machining operations, edit tools & toolpaths, turn on/off operations, and reorder the machining sequence for greater efficiency.
Dynamic Machining Strategies™ (DMS™)
DMS™ allows users to apply any number of machining operations to a single CAD model feature. This feature allows you to load single or multiple machining strategies into one operation inside of the CAM job tree. For instance, you can apply roughing, semi-finishing and finishing operations to a feature within a single operation and easily edit these on the fly. This allows you to keep all of your operations for a single feature in one spot for simple organization. These operations can then be easily reapplied on other features, as needed.
Selection Tools
The selection tool is equipped with powerful performance features to make selections quicker and easier.
Layers – Layers are a user-friendly feature geared towards making the design process easier to navigate. The software allows you to select and segment out geometry sections and organize them into separate layers. At any time layers can be turned on or off to enable complete visibility control of the part. The “select by layer” option allows you to quickly select your geometry.
Colors – Geometry selections can be given color assignments to make identifying part segments easier. Using the “select by color” option allows you to select part segments by color assignments without the use of layers.
Reduce, Reuse, Recycle Operations
As is the case with many shops, jobs can often be very similar in nature. Instead of starting over for each part job, CAM programming technology allows you to reuse and recycle machining operations along with any machine, tool, and tool holder set ups that were used on previous CAM jobs. As you perform more jobs with CAM, the reduced number of steps can have a bit of a “snowball” effect in terms of time savings gleaned from your ability to reuse operations from previous jobs.
Simulation
Without CAM programming technology, a programmer is forced to rely more heavily on machine trial runs to verify they’ve correctly programmed their machine operations.
Realistic simulations can provide some pretty significant efficiency, time savings, and profitability benefits. Within the CAM software, users can evaluate and use the following:
Part Deviation Analysis – Color coded tolerance levels identify various areas on the part that the tool left excess material. Tools or toolpaths can be adjusted based on this feedback.
Dynamic Viewing Functionality – The user has control over transparency levels for everything from the machine, tool, and part sections to see the part from any angle at any point during the simulation.
Check for Errors – The simulation will pinpoint potential machine, tool, and tool holder collisions and part gouges which helps to eliminate costly programming errors before they ever reach the machine.
Calculate Cycle Times – Know how long it will take to run your job to help plan your production schedule.
CAM programming technology has reached a tipping point. Not using it seriously impacts a shop’s ability to effectively compete in the average marketplace.
Discover the capabilities of CAM programming technology for yourself with a free demo download of the powerful BobCAD-CAM software. CLICK HERE TO DOWNLOAD.
Other related CAD-CAM articles that you may be interested in:
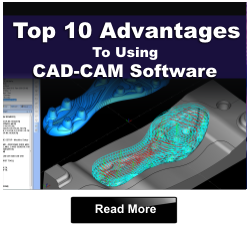
Summary
Article Name
CAM Programming Technology Guaranteed to Increase CNC Program Efficiency
Description
When it comes to shop efficiency, productivity, and profitability, CAM programming technology is equally as important as the machines and tools it helps to program.
Author
Nick Erickson | BobCAD-CAM